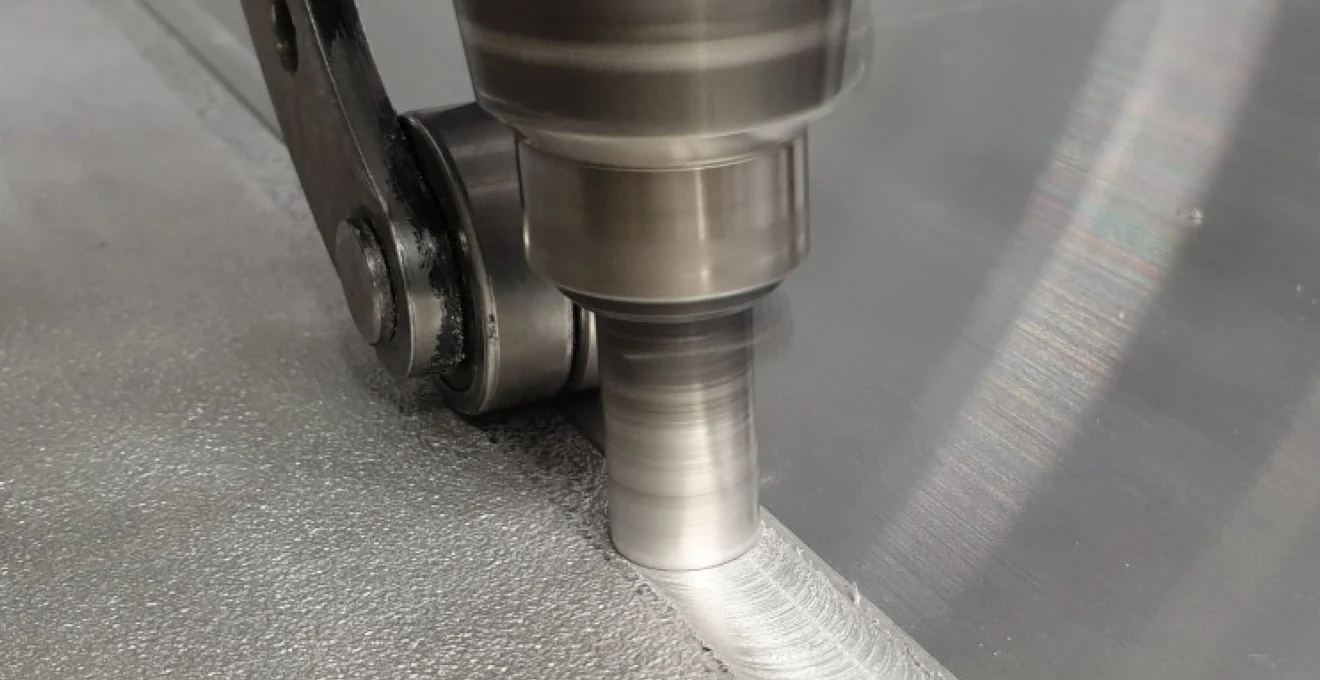
Friction stir welding (FSW) has revolutionized the joining of metals, particularly in industries where high-strength, defect-free welds are crucial. As this innovative technique continues to gain traction, the proper maintenance and calibration of FSW equipment become paramount. Ensuring the optimal performance of these sophisticated machines not only extends their lifespan but also guarantees consistent, high-quality welds that meet stringent industry standards.
Principles of friction stir welding equipment maintenance
Maintaining friction stir welding equipment requires a comprehensive understanding of its components and operational principles. The cornerstone of effective FSW maintenance lies in regular inspections, proactive servicing, and adherence to manufacturer guidelines. By implementing a robust maintenance strategy, you can significantly reduce downtime, enhance weld quality, and optimize the overall efficiency of your FSW operations.
One of the primary aspects of FSW equipment maintenance is the preservation of the tool's integrity. The rotating tool, responsible for generating frictional heat and material flow, undergoes substantial wear during the welding process. Regular assessment of tool geometry, surface condition, and material composition is essential to maintain optimal performance. Additionally, the spindle and its associated bearings require meticulous attention to ensure smooth rotation and precise control over the welding process.
Another critical area of focus is the machine's structural components. The rigidity and alignment of the FSW system directly impact weld quality. Periodic checks for any signs of wear, deformation, or misalignment in the machine frame, traversing mechanism, and clamping systems are vital. These inspections help prevent issues that could compromise weld integrity or lead to equipment failure.
Calibration techniques for FSW machines
Calibration is a fundamental aspect of FSW equipment maintenance that ensures accuracy, repeatability, and quality in the welding process. Precise calibration of various parameters is essential for achieving optimal weld characteristics and maintaining consistency across production runs. Let's delve into the key calibration techniques for different components of FSW machines.
Tool rotation speed calibration using tachometers
The rotation speed of the FSW tool is a critical parameter that influences heat generation and material flow. Calibrating the tool rotation speed involves the use of high-precision tachometers to verify and adjust the spindle's rotational velocity. This process typically includes:
- Mounting a calibrated tachometer to the spindle
- Comparing the measured speed with the machine's display
- Adjusting the control system to align with the actual speed
- Verifying calibration across the entire operational speed range
It's important to note that rotation speed calibration should be performed under various load conditions to ensure accuracy during actual welding operations.
Axial force calibration with load cells
The axial force applied by the FSW tool is crucial for proper material consolidation and weld formation. Calibrating the axial force measurement system involves the use of precision load cells. The process typically includes:
- Installing a calibrated load cell between the tool and workpiece
- Applying a range of known forces
- Comparing the machine's force readings with the load cell measurements
- Adjusting the force measurement system to match the calibrated values
- Verifying linearity and repeatability across the operational force range
Accurate force calibration ensures that the welding parameters remain consistent and that the correct pressure is applied throughout the weld process.
Traverse speed adjustment for optimal weld quality
The traverse speed of the FSW tool along the weld line significantly impacts weld quality and cycle time. Calibrating the traverse speed involves:
- Using precision linear encoders or laser interferometers
- Measuring actual tool movement over a known distance
- Comparing measured speed with the machine's set speed
- Fine-tuning the motion control system for accuracy
Proper calibration of traverse speed ensures consistent heat input and material flow, resulting in uniform weld properties along the entire joint length.
Temperature monitoring system calibration
Accurate temperature measurement is essential for process control and weld quality assurance in FSW. Calibrating the temperature monitoring system typically involves:
- Using calibrated thermocouples or pyrometers
- Placing calibration devices at key points in the weld zone
- Comparing readings from the machine's sensors with calibrated instruments
- Adjusting sensor settings or applying correction factors as needed
- Verifying temperature readings across the expected operational range
Properly calibrated temperature monitoring systems allow for precise control of heat input and help prevent overheating or insufficient heating during the welding process.
Critical components requiring regular inspection
To maintain the performance and longevity of FSW equipment, certain critical components demand regular inspection and maintenance. These components are subject to high stress and wear during the welding process, and their condition directly impacts weld quality and machine reliability.
FSW tool wear assessment and replacement criteria
The FSW tool is perhaps the most crucial component in the welding process. Regular assessment of tool wear is essential for maintaining weld quality. Key aspects to consider include:
- Measuring changes in tool geometry (e.g., pin length, shoulder diameter)
- Inspecting for surface defects or material buildup
- Evaluating tool material integrity and potential for failure
- Establishing clear criteria for tool replacement based on wear limits or weld quality indicators
Implementing a systematic tool wear assessment program helps prevent sudden failures and ensures consistent weld properties throughout production runs.
Spindle bearing lubrication and alignment checks
The spindle and its bearings are critical for maintaining precise tool control and rotation. Regular maintenance of these components includes:
- Checking and replenishing lubricants according to manufacturer specifications
- Monitoring bearing temperatures during operation for signs of wear or insufficient lubrication
- Performing vibration analysis to detect early signs of bearing wear or misalignment
- Verifying spindle runout and correcting any deviations from acceptable tolerances
Proper spindle maintenance is crucial for achieving smooth tool rotation and preventing premature wear of other system components.
Backing plate flatness and surface integrity evaluation
The backing plate provides support for the workpiece and influences heat dissipation during welding. Regular inspection of the backing plate involves:
- Measuring surface flatness using precision instruments
- Inspecting for signs of wear, deformation, or damage
- Evaluating the condition of any cooling channels or temperature control systems
- Resurfacing or replacing the backing plate when flatness or surface integrity is compromised
Maintaining a flat and stable backing plate is essential for achieving consistent weld quality and preventing defects caused by improper workpiece support.
Clamping system pressure and uniformity verification
The clamping system secures the workpieces during welding and plays a crucial role in preventing distortion. Regular checks of the clamping system include:
- Verifying clamp pressure using calibrated pressure gauges
- Ensuring uniform pressure distribution across the workpiece
- Inspecting clamp surfaces for wear or damage that could affect grip
- Testing clamp actuation and release mechanisms for proper function
Proper clamping is essential for maintaining weld joint alignment and preventing workpiece movement during the welding process.
Advanced diagnostic tools for FSW equipment
As FSW technology continues to evolve, so do the diagnostic tools used to maintain and optimize these systems. Advanced diagnostic equipment allows for more precise monitoring and troubleshooting of FSW machines, enabling proactive maintenance and rapid problem resolution.
One of the most valuable diagnostic tools in modern FSW systems is the real-time process monitoring system. These sophisticated systems continuously track critical welding parameters such as forces, temperatures, and tool position. By analyzing this data, operators can identify trends or anomalies that may indicate impending issues or opportunities for process optimization.
Another powerful diagnostic tool is vibration analysis equipment. By measuring and analyzing the vibrations produced during the welding process, technicians can detect early signs of bearing wear, spindle misalignment, or other mechanical issues. This allows for targeted maintenance interventions before these problems can affect weld quality or cause equipment failure.
Thermal imaging cameras have also become indispensable in FSW diagnostics. These devices provide a visual representation of heat distribution across the weld zone and machine components. By identifying hotspots or unusual thermal patterns, operators can quickly pinpoint areas of concern, such as insufficient cooling or excessive friction in mechanical components.
Preventive maintenance schedules for FSW systems
Implementing a comprehensive preventive maintenance schedule is crucial for maximizing the reliability and performance of FSW systems. These schedules should be tailored to the specific equipment and operational demands of your facility. Let's explore the key components of an effective preventive maintenance program for FSW equipment.
Daily Pre-Operation checklists for FSW operators
Daily checks performed by operators are the first line of defense against equipment issues. A typical daily checklist might include:
- Visual inspection of the tool and clamping system
- Verification of coolant levels and flow rates
- Check for any unusual noises or vibrations during startup
- Confirmation of proper machine warm-up procedures
- Brief test run to ensure all systems are functioning correctly
These quick, routine checks can help identify potential problems before they escalate, ensuring that the equipment is ready for the day's production.
Monthly maintenance procedures for mechanical components
Monthly maintenance tasks focus on more in-depth inspections and servicing of mechanical components. These procedures typically include:
- Detailed inspection of the FSW tool and replacement if necessary
- Lubrication of all moving parts according to the manufacturer's specifications
- Checking and adjusting belt tensions where applicable
- Inspection and cleaning of cooling system components
- Verification of machine alignment and calibration
Regular monthly maintenance helps prevent unexpected breakdowns and ensures consistent machine performance over time.
Quarterly electrical system and control panel inspections
Electrical systems and control panels require periodic attention to maintain reliability. Quarterly inspections should include:
- Checking all electrical connections for tightness and signs of corrosion
- Inspecting wiring insulation for damage or wear
- Testing emergency stop functions and safety interlocks
- Verifying proper function of all sensors and feedback systems
- Updating control software if necessary
These inspections help prevent electrical failures that could lead to extended downtime or safety hazards.
Annual comprehensive FSW machine overhaul protocol
An annual overhaul provides an opportunity for thorough inspection and refurbishment of the entire FSW system. This comprehensive process typically includes:
- Complete disassembly and inspection of major components
- Replacement of worn bearings, seals, and other critical parts
- Recalibration of all measurement and control systems
- Verification of machine geometry and realignment if necessary
- Thorough cleaning and repainting of machine surfaces
- Comprehensive system tests to ensure optimal performance
The annual overhaul is crucial for extending the life of the FSW equipment and maintaining peak performance year after year.
Troubleshooting common FSW equipment issues
Even with rigorous maintenance protocols, FSW equipment may occasionally experience issues that require troubleshooting. Developing a systematic approach to problem-solving can minimize downtime and ensure rapid resolution of common problems.
One frequent issue in FSW operations is inconsistent weld quality. This can often be traced back to variations in tool wear, improper force application, or fluctuations in rotational speed. To troubleshoot these issues:
- Review recent process monitoring data for any deviations from normal parameters
- Inspect the FSW tool for signs of excessive wear or damage
- Verify force sensor calibration and adjust if necessary
- Check spindle bearings for any signs of wear or play
By systematically addressing these common issues, you can maintain the performance and reliability of your FSW equipment, ensuring consistent production of high-quality welds. Remember that proper documentation of troubleshooting processes and outcomes can provide valuable insights for future maintenance and optimization efforts.